Industrial Cleaning Services
Keep your equipment and your business running smoothly.
- COVID Sanitation
- Silos
- Ductwork
- Walls and Ceilings
- Pressure Washing
- Confined Spaces
- Cooling Towers
Blackwell’s, Inc. continues with COVID preparedness and prevention readiness.
With the high levels of vaccine and infection-induced immunity, and the availability of new treatments for COVID, the risk for illness, hospitalization, and death have been greatly reduced. Even so, disinfection practices are still important for isolated cases in publicly accessible buildings.
Our protocol initially established on March 7, 2020, has been modified to reflect updated CDC guidelines and information about the virus. Modifications will continue as more information becomes known.
Blackwell’s, Inc. Industrial Cleaning has purchased additional foggers, and EPA approved sanitization chemicals have been stockpiled by our company to prevent availability service disruptions from impacting clientele.
Duct cleaning and duct sanitizing equipment modifications make our duct cleaning process even more effective in removing particulate attachment media within ducts. Fumigation of ductwork interior surfaces have also been enhanced both mechanically and chemically.
The economical chemical fogging process we are using allows our customers to re-occupy sanitized space within 45 minutes of application. This is based on good air movement. The fogging process is literally a slow walk through the area.
Please know, we are here to help you continue to work safely and productively. Keep Blackwell’s, Inc. in mind should the need arise.
We will all get through this if we continue to work together.

Cleaning ovens and ductwork
HVAC and Ductwork Cleaning:
- Initial cleaning to remove debris
- Ductwork systems fogged with sanitizer registered by the EPA specifically for ductwork
- Common areas, frequently touched hard, non-porous surfaces, and walls typically up to 8 ft. or above, are treated with EPA approved germicidal disinfectant.
Food Processing Facilities:
Walls and hard surfaces in food handling and processing areas in schools, dairies, restaurants, and USDA inspected facilities, are treated with sanitizer approved by the EPA for these areas.
Procedures to Contain the Virus:
- Staging and decontamination for our cleaning and sanitizing teams take place in negative pressure containment areas
- Cleaned and sanitized areas are barricaded and posted with re-entry times to prevent re-introducing contamination to these areas
We will continue to monitor the Centers for Disease Control and the Environmental Protection Agency guidelines, in a front-line position in the fight against COVID.
Regardless of what a silo holds, there will come a time when it will require industrial cleaning service.
Cleaning is necessary to:
- Remove the buildup of old product that reduces the volume of the silo
- Dislodge wall or cone buildup that impedes the flow of product to the auger or pneumatic conveyance and increases the likely hood of “bridging”
- Allow for inspection of the silo to determine areas needing repair
- Control sources of contaminants in the silo
- Help prevent insect infestation
Dangers associated with the confined space cleaning of silos:
- Falls resulting from the use of inadequate safety equipment and/or training in the use of the equipment
- Spontaneous combustion due to suspended particulate matter
- Depleted oxygen levels and/or noxious gases
- Entrapment in the product due to voids created from product “bridging” in the silo and the potential collapse of the product.
The advantages of blast cleaning food silos with CO2 instead of pressure washing:
- Mold growth is inhibited because no water is used
- Silo surfaces are decontaminated
- No secondary waste stream-food silo residues can be removed by vacuum
- Drastic measures are sometimes needed to prevent contamination of the finished product in silos. Even when design specifications are followed during construction, inspections of an aging silo can uncover a lining failure of the wall that can cause the product in the silo to be unfit for its intended use. A repair of the wall lining is especially important in a food product silo. Scope of Work to Repair a Food Silo Lining
- Follow all confined space protocol using Blackwell’s, Inc. OSHA certified associates
- Remove any remaining product to allow for inspection of the silo to determine areas needing repair (Vacuum truck available if needed)
- Construct a negative air barricade to prevent cross-contamination (if inside a facility)
- Use hot water/high pressure wash cleaning of interior walls
- Collect and dispose of liquid waste effluent from the pressure washing
- Mechanically hand grind the coating failure areas to SSPC specifications
- Apply an FDA approved penetrating epoxy primer to prevent flash rusting
- Apply a 100% solids coating material for steel creating a suitable wear and bond coat
- Apply FDA approved high performance and abrasive resistant tank lining.
- A final hot water/high pressure washing and drying completes the repair
Manufacturing typically creates all kinds of dust, smoke, mists, or any number of different particulates.
These contaminants are removed from the manufacturing facility through an exhaust system which ideally filters the exhaust air before it is released back into the atmosphere. Over time, these contaminants can build up in the exhaust ductwork itself.
For plants in continuous production, these systems require preventive maintenance.
Problems associated with contaminant buildup in the ductwork and air handlers:
- Restriction of airflow
- Risk of fire hazard
- Illness from breathing contaminated plant air
- Contaminants being released into the atmosphere
These problems affect the system by:
- Increasing maintenance costs
- Increasing the frequency of shutdowns for repair and/or replacement of components
- Decreasing the efficiency of the system and increasing energy consumption
- Posing a potential liability associated with illness due to breathing contaminated plant air
- Environmental liability due to release of contaminated air.
Contaminants in the ventilation system are hidden. You probably don't see it but it can be there.
OSHA recommends a routine regular inspection of supply, exhaust, return grilles, and ductwork (at least semi-annually). Heavily fouled ductwork not only impedes the airflow and restricts the ventilation, but it also increases energy costs and increases the risk of a system failure in the industrial facility.

Contaminant removed and ductwork reassembled

This ductwork required disassembly to remove the contaminants.
When it comes to keeping your industrial facility clean, walls and ceilings are commonly missed.
Don't overlook these surfaces in your industrial business. Schedule an industrial cleaning service for your walls and ceilings to create a smooth, functional workspace. Our team is trained and certified to clean your industrial surfaces, no matter what type of industry you're in.
Keeping your industrial space clean is a big job. However, the walls and ceiling tend to get overlooked, which can be hazardous. The health and safety of your employees is important to keep In mind when maintaining your facility and maintaining low employee turnover.
From smoke, dust and grease to mold and mildew, harmful particles can build up on your walls and ceiling, creating a dangerous environment, and reducing employee morale. 175 fires and 37 explosions caused by dust is just one example of the negative impact of a dirty industrial facility.
C02 blasting, compressed air, pressure washing and a bottle and rag are the ways that Blackwell’s can solve your cleaning needs.
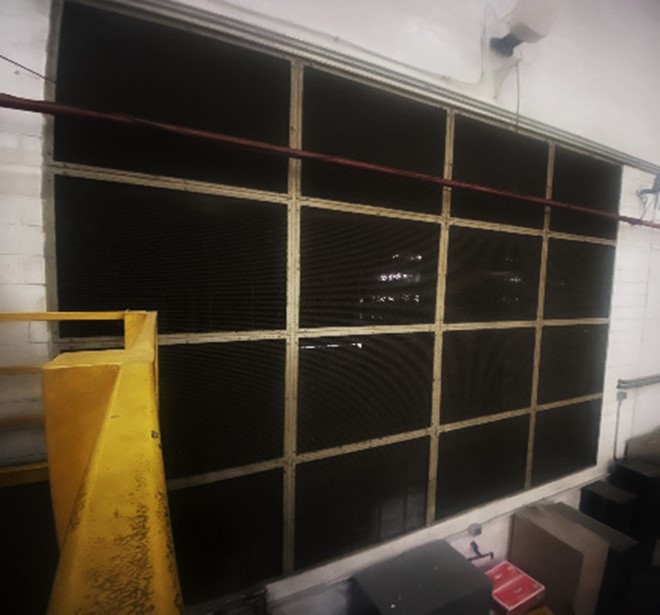

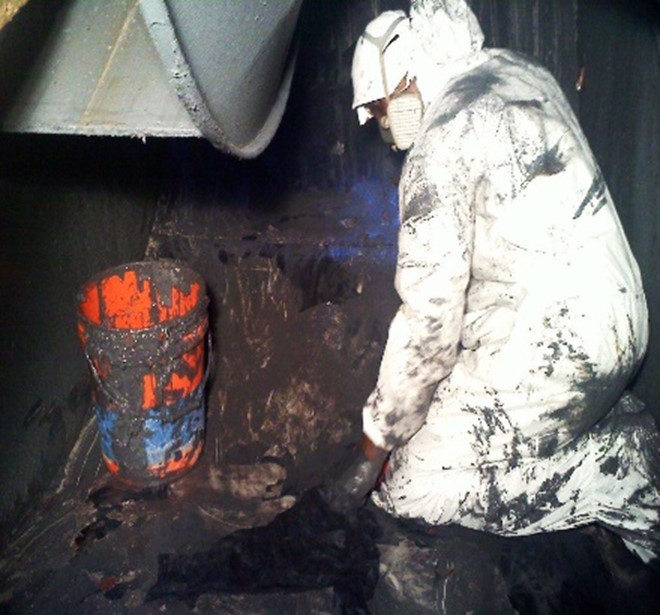
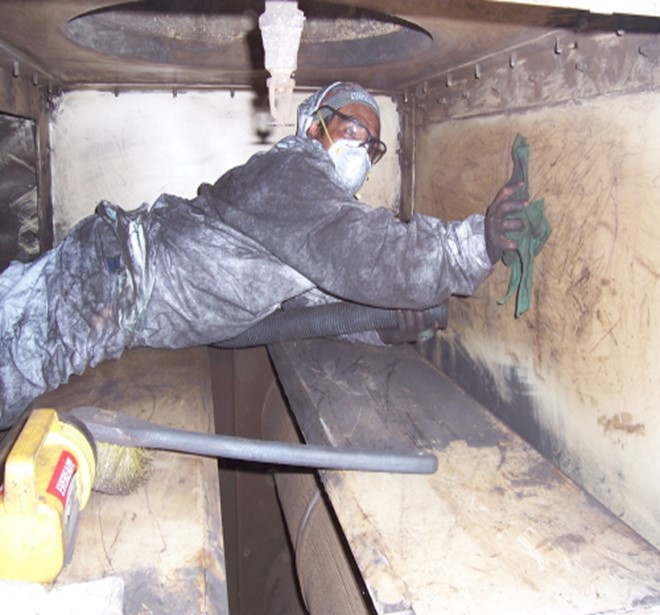
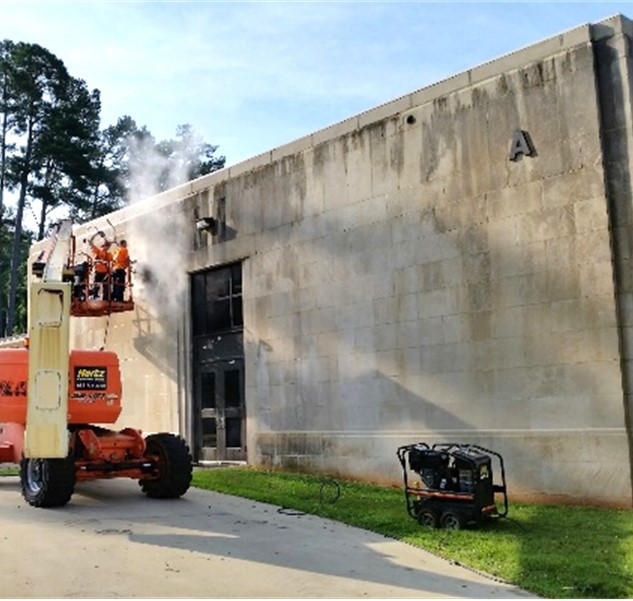
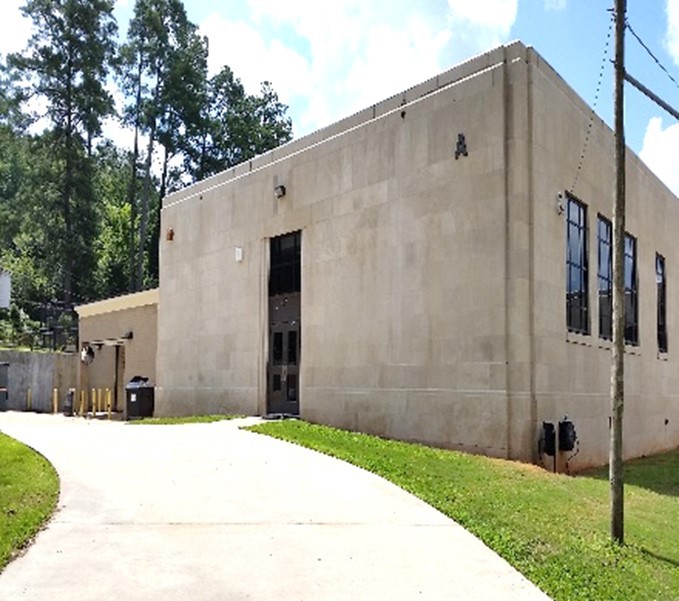
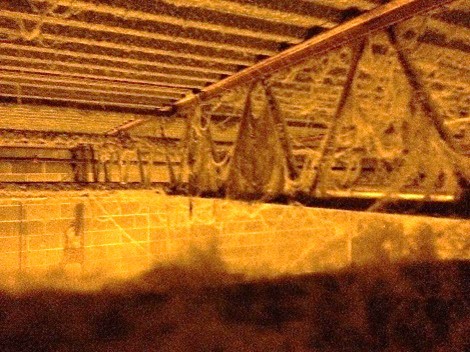
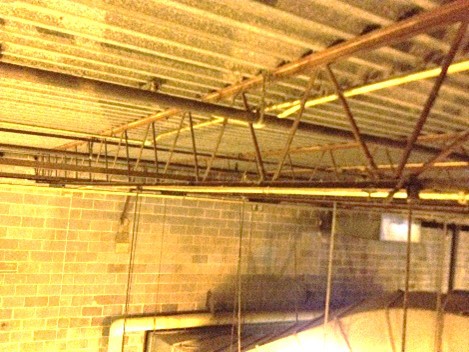
Call Blackwell's, Inc. Industrial Cleaning for all your pressure washing needs.
Our high-tech equipment can get even the roughest surfaces clean. You know how important it is to keep your industrial space clean, let us do the dirty work so you can get back to business.
- 3,000 to 4,000 PSI
- 4 to 8 gallons
- 100 to 200 degrees F
- Hot or cold water
- Improve the curb appeal of your industrial facility
- Reduce the need for costly repairs
- Improve working environment
- Protect against mold, dirt, and grime build up
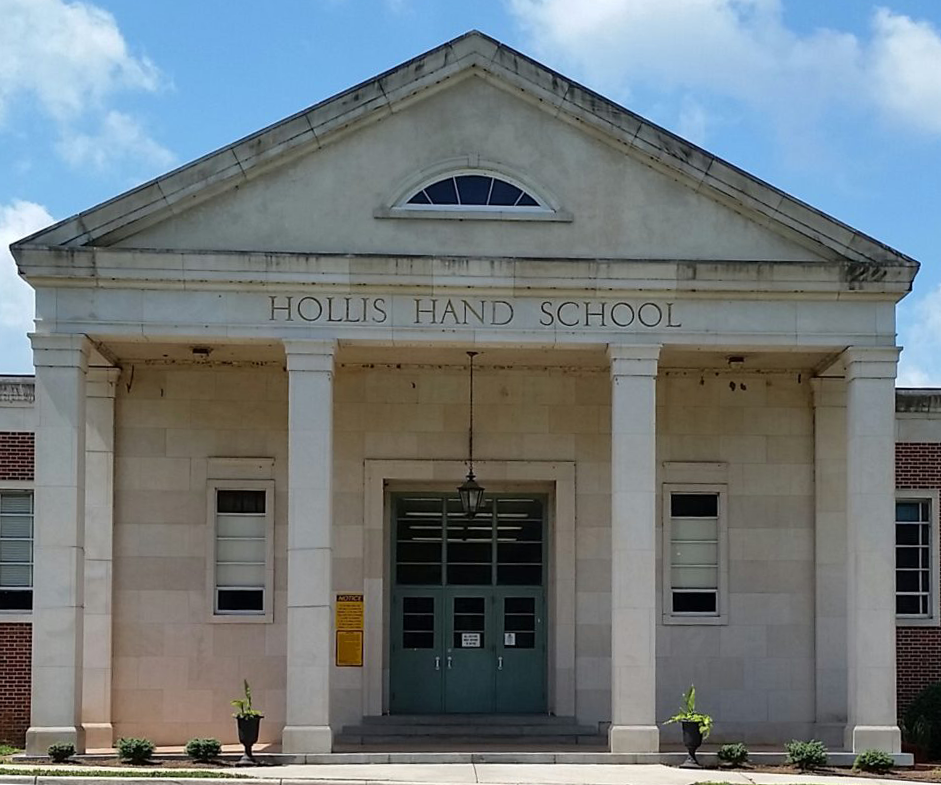
Pressure washing (After)
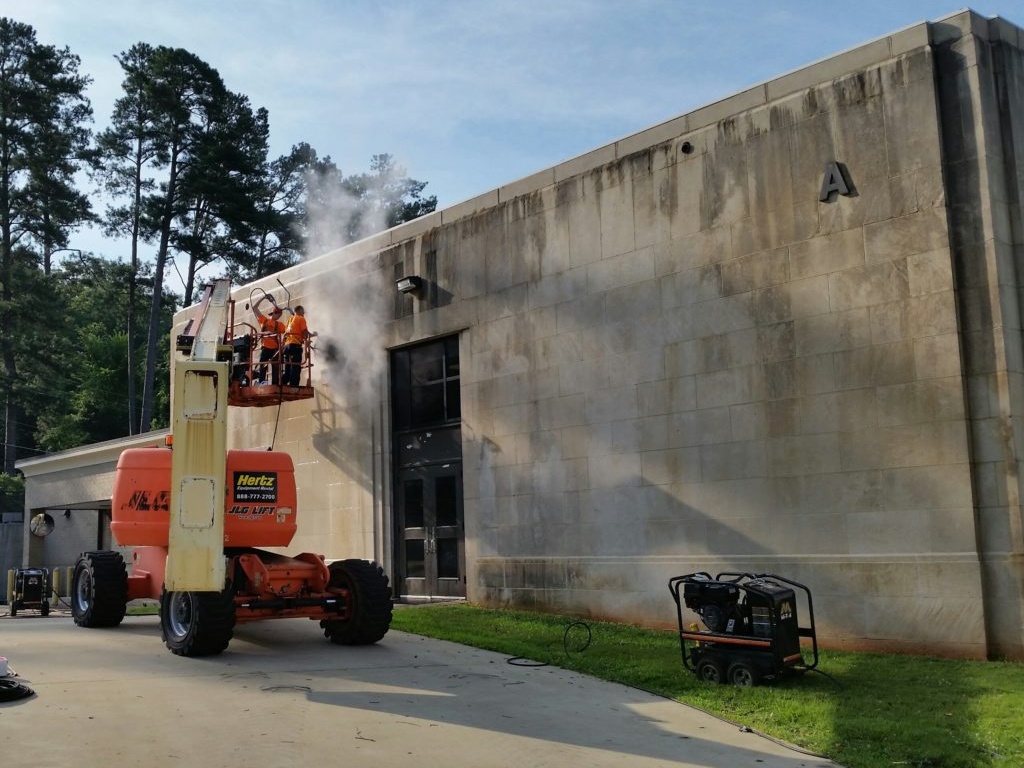
Pressure washing (After)
See Our Industrial Cleaning Service in Action
- Is large enough that an employee can enter and perform work
- Has limited or restricted means for entry or exit
- Is not designed for continuous employee occupancy
- Contains or may contain a hazardous atmosphere
- Contains a material that has the potential for engulfing an entrant
- Is shaped such that an entrant could be trapped or asphyxiated
- Contains any other serious safety or health hazards
Confined Spaces include tanks, storage bins, pits, silos, ovens, and ductwork 25% of confined spaces have hazardous air. 50% of deaths in confined spaces result from oxygen deficiency (or limited air supply) and no air monitoring. Blackwell’s, Inc. Protocol for Safety in Confined Spaces:
- Complete Confined Space Permit
- Control the Access Zone (barricades/fall protection)
- Monitor the air quality with Multi Gas Detector (O2, H2S, CO, LEL)
- Provide natural or mechanical ventilation as needed
- PPE required: Tyvek suit, gloves, eye and ear protection, dust mask (or APR/SAR if needed)
- Vertical work: tripod, winches, safety harness
- Horizontal work: anklets attached to safety retrieval line
- Attendant: continuously observes and communicates with entrant
4 Basic Steps We Take to Protect Our Associates
- Identify any confined spaces in the workplace
- Risk assessment of all hazards in those confined spaces
- Take all necessary steps to mitigate the identified hazards
- Put in to place an established rescue plan for emergencies
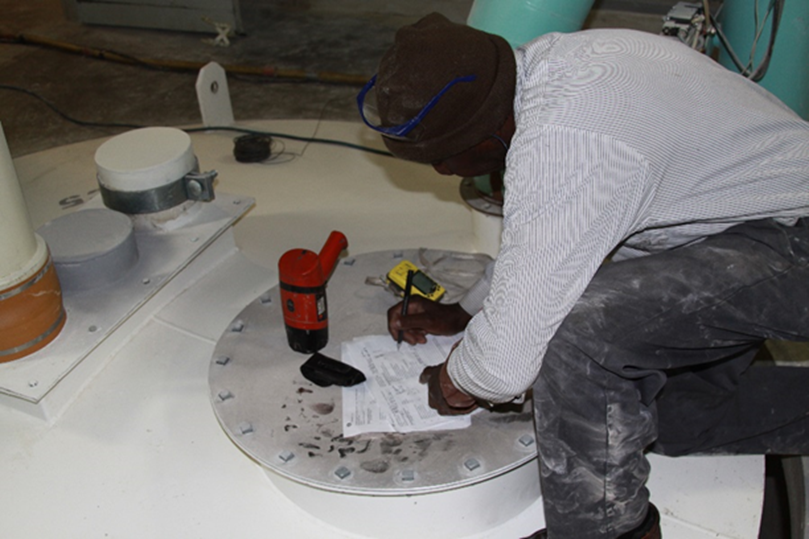
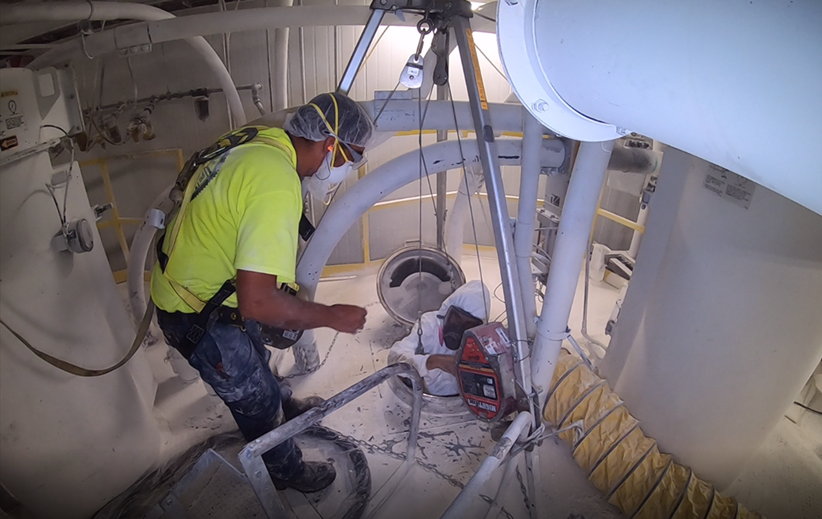
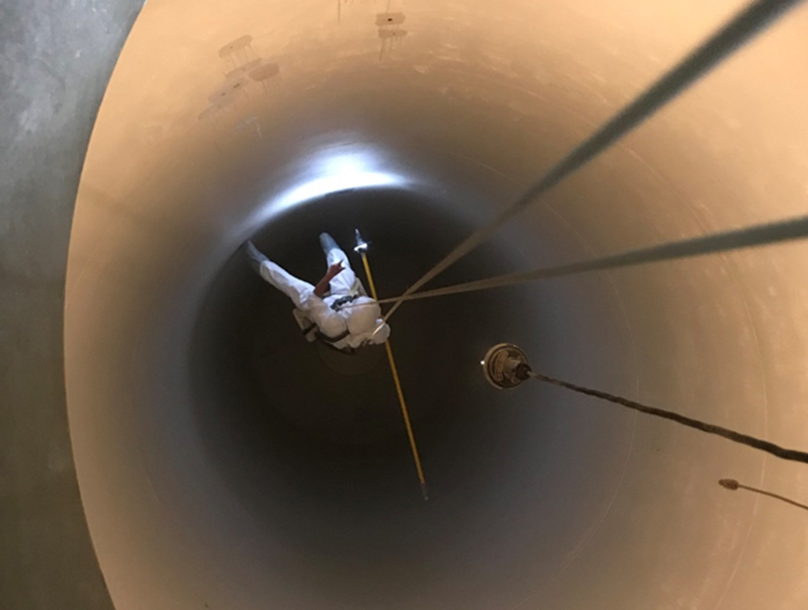
Cooling towers are specialized heat exchanging devices to cool water and dissipate heat to the atmosphere.
For plants in continuous production, these systems require preventive maintenance.
Problems associated with cooling water systems:
- Corrosion from oxidation of the metal components of system
- Scale buildup from precipitation of minerals in water
- Fouling from dust and corrosion by-products
- Microbial contamination (bacteria, yeasts, fungi, algae) creating waste deposits (microbial slime) and potential contagions (e.g. Legionella)
- Animal excrement buildup (e.g. pigeons) and disease associated with atomization and respiration of contaminated water
These problems affect the system by:
- Increasing maintenance costs
- Increasing the frequency of shutdowns for repair and/or replacement of components
- Decreasing the cooling efficiency and increasing energy consumption
- Posing a potential liability associated with illness due to lack of cleaning or maintenance of the cooling tower
- COVID Sanitation
- Silos
- Ductwork
- Walls and Ceilings
- Pressure Washing
- Confined Spaces
- Cooling Towers
Blackwell’s, Inc. continues with Covid-19 preparedness and prevention readiness.
Our protocol initially established on March 7, 2020, has been modified to reflect updated CDC guidelines and information about the virus. Modifications will continue as more information becomes known. Blackwell’s has purchased additional foggers, and EPA approved sanitization chemicals have been stockpiled by our company to prevent availability service disruptions from impacting clientele. Duct cleaning and duct sanitizing equipment modifications make our duct cleaning process even more effective in removing particulate attachment media within ducts. Fumigation of ductwork interior surfaces have also been enhanced both mechanically and chemically. The economical chemical fogging process we are using allows our customers to re-occupy sanitized space within 45 minutes of application. This is based on good air movement. The fogging process is literally a slow walk through the area. Please know, we are here to help you continue to work safely and productively. Keep Blackwell’s, Inc. in mind should the need arise. We will all get through this if we continue to work together.
Cleaning ovens and ductwork
HVAC and Ductwork Cleaning:
- Initial cleaning to remove debris
- Ductwork systems fogged with sanitizer registered by the EPA specifically for ductwork
- Common areas, frequently touched hard, non-porous surfaces, and walls typically up to 8 ft. or above, are treated with EPA approved germicidal disinfectant.
Food Processing Facilities:
Walls and hard surfaces in food handling and processing areas in schools, dairies, restaurants, and USDA inspected facilities, are treated with sanitizer approved by the EPA for these areas.Procedures to Contain the Virus:
- Staging and decontamination for our cleaning and sanitizing teams take place in negative pressure containment areas
- Cleaned and sanitized areas are barricaded and posted with re-entry times to prevent re-introducing contamination to these areas
Regardless of what a silo holds, there will come a time when it will have to be cleaned.
Cleaning is necessary to:- Remove the buildup of old product that reduces the volume of the silo
- Dislodge wall or cone buildup that impedes the flow of product to the auger or pneumatic conveyance and increases the likely hood of “bridging”
- Allow for inspection of the silo to determine areas needing repair
- Control sources of contaminants in the silo
- Help prevent insect infestation
- Falls resulting from the use of inadequate safety equipment and/or training in the use of the equipment
- Spontaneous combustion due to suspended particulate matter
- Depleted oxygen levels and/or noxious gases
- Entrapment in the product due to voids created from product “bridging” in the silo and the potential collapse of the product.
- Mold growth is inhibited because no water is used
- Silo surfaces are decontaminated
- No secondary waste stream-food silo residues can be removed by vacuum
- Drastic measures are sometimes needed to prevent contamination of the finished product in silos. Even when design specifications are followed during construction, inspections of an aging silo can uncover a lining failure of the wall that can cause the product in the silo to be unfit for its intended use. A repair of the wall lining is especially important in a food product silo. Scope of Work to Repair a Food Silo Lining
- Follow all confined space protocol using Blackwell’s, Inc. OSHA certified associates
- Remove any remaining product to allow for inspection of the silo to determine areas needing repair (Vacuum truck available if needed)
- Construct a negative air barricade to prevent cross-contamination (if inside a facility)
- Use hot water/high pressure wash cleaning of interior walls
- Collect and dispose of liquid waste effluent from the pressure washing
- Mechanically hand grind the coating failure areas to SSPC specifications
- Apply an FDA approved penetrating epoxy primer to prevent flash rusting
- Apply a 100% solids coating material for steel creating a suitable wear and bond coat
- Apply FDA approved high performance and abrasive resistant tank lining.
- A final hot water/high pressure washing and drying completes the repair
- Drastic measures are sometimes needed to prevent contamination of the finished product in silos. Even when design specifications are followed during construction, inspections of an aging silo can uncover a lining failure of the wall that can cause the product in the silo to be unfit for its intended use. A repair of the wall lining is especially important in a food product silo. Scope of Work to Repair a Food Silo Lining
- Follow all confined space protocol using Blackwell’s, Inc. OSHA certified associates
- Remove any remaining product to allow for inspection of the silo to determine areas needing repair (Vacuum truck available if needed)
- Construct a negative air barricade to prevent cross-contamination (if inside a facility)
- Use hot water/high pressure wash cleaning of interior walls
- Collect and dispose of liquid waste effluent from the pressure washing
- Mechanically hand grind the coating failure areas to SSPC specifications
- Apply an FDA approved penetrating epoxy primer to prevent flash rusting
- Apply a 100% solids coating material for steel creating a suitable wear and bond coat
- Apply FDA approved high performance and abrasive resistant tank lining.
- A final hot water/high pressure washing and drying completes the repair
Manufacturing typically creates all kinds of dust, smoke, mists, or any number of different particulates.
These contaminants are removed from the manufacturing facility through an exhaust system which ideally filters the exhaust air before it is released back into the atmosphere. Over time, these contaminants can build up in the exhaust ductwork itself.
For plants in continuous production, these systems require preventive maintenance.
Problems associated with contaminant buildup in the ductwork and air handlers:
- Restriction of airflow
- Risk of fire hazard
- Illness from breathing contaminated plant air
- Contaminants being released into the atmosphere
These problems affect the system by:
- Increasing maintenance costs
- Increasing the frequency of shutdowns for repair and/or replacement of components
- Decreasing the efficiency of the system and increasing energy consumption
- Posing a potential liability associated with illness due to breathing contaminated plant air
- Environmental liability due to release of contaminated air
Contaminants in the ventilation system are hidden. You probably don't see it but it can be there. OSHA recommends a routine regular inspection of supply, exhaust, return grilles, and ductwork (at least semi-annually).
Heavily fouled ductwork not only impedes the airflow and restricts the ventilation, but it also increases energy costs and increases the risk of a system failure in the industrial facility.

The ductwork at this industrial facility was disassembled to clean the contaminant buildup
When it comes to keeping your industrial facility clean, walls and ceilings are commonly missed.
Don't overlook these surfaces in your industrial business. Schedule a cleaning of your walls and ceilings to create a smooth, functional workspace. Our team is trained and certified to clean your industrial surfaces, no matter what type of industry you're in. Keeping your industrial space clean is a big job. However, the walls and ceiling tend to get overlooked, which can be hazardous. The health and safety of your employees is important to keep In mind when maintaining your facility and maintaining low employee turnover. From smoke, dust and grease to mold and mildew, harmful particles can build up on your walls and ceiling, creating a dangerous environment, and reducing employee morale. 175 fires and 37 explosions caused by dust is just one example of the negative impact of a dirty industrial facility. C02 blasting, compressed air, pressure washing and a bottle and rag are the ways that Blackwell’s can solve your cleaning needs.Call Blackwell's for all your pressure washing needs.
Our high-tech equipment can get even the roughest surfaces clean. You know how important it is to keep your industrial space clean, let us do the dirty work so you can get back to business.- 3,000 to 4,000 PSI
- 4 to 8 gallons
- 100 to 200 degrees F
- Hot or cold water
- Improve the curb appeal of your industrial facility
- Reduce the need for costly repairs
- Improve working environment
- Protect against mold, dirt, and grime build up
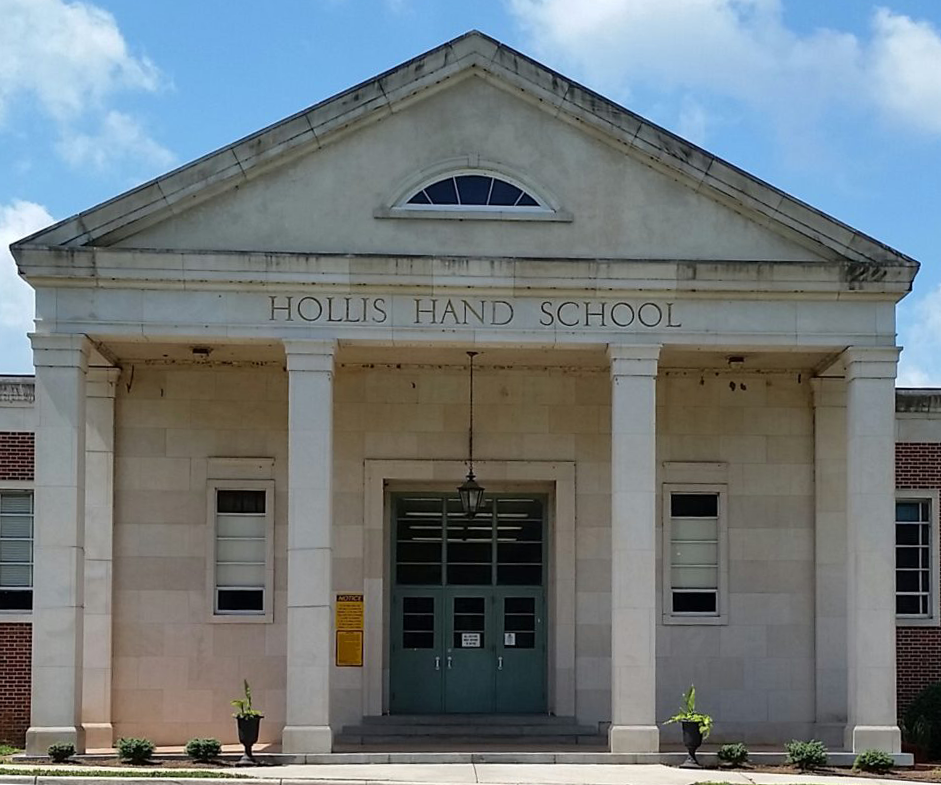
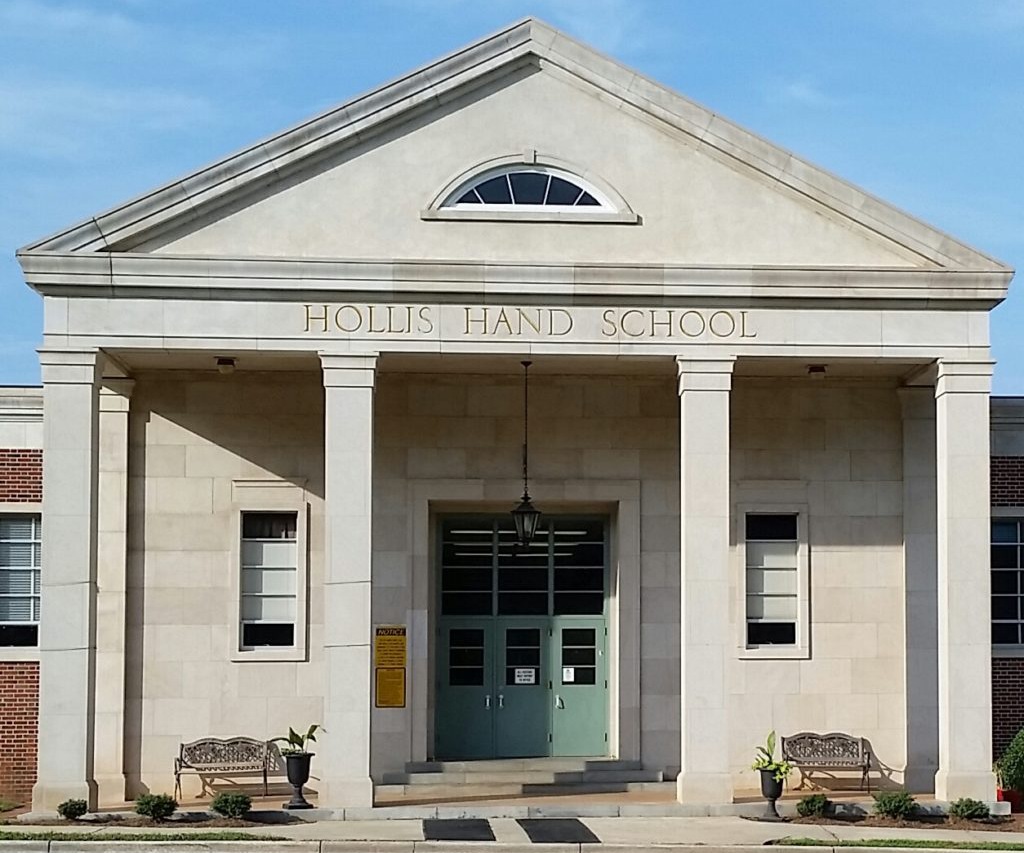
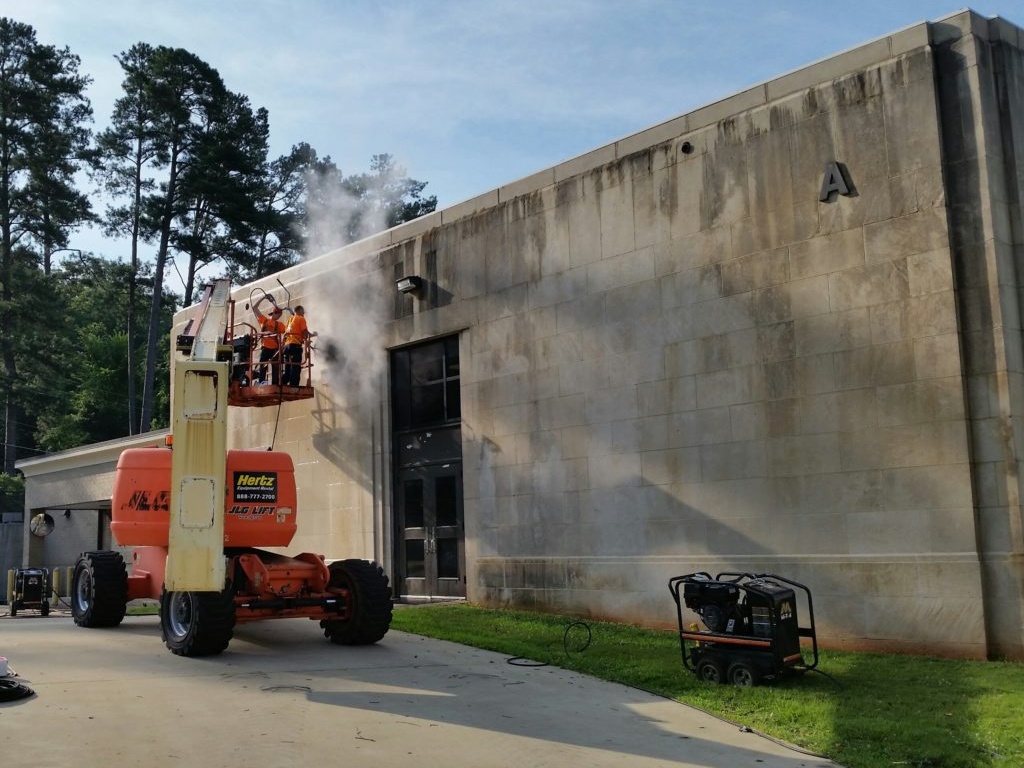
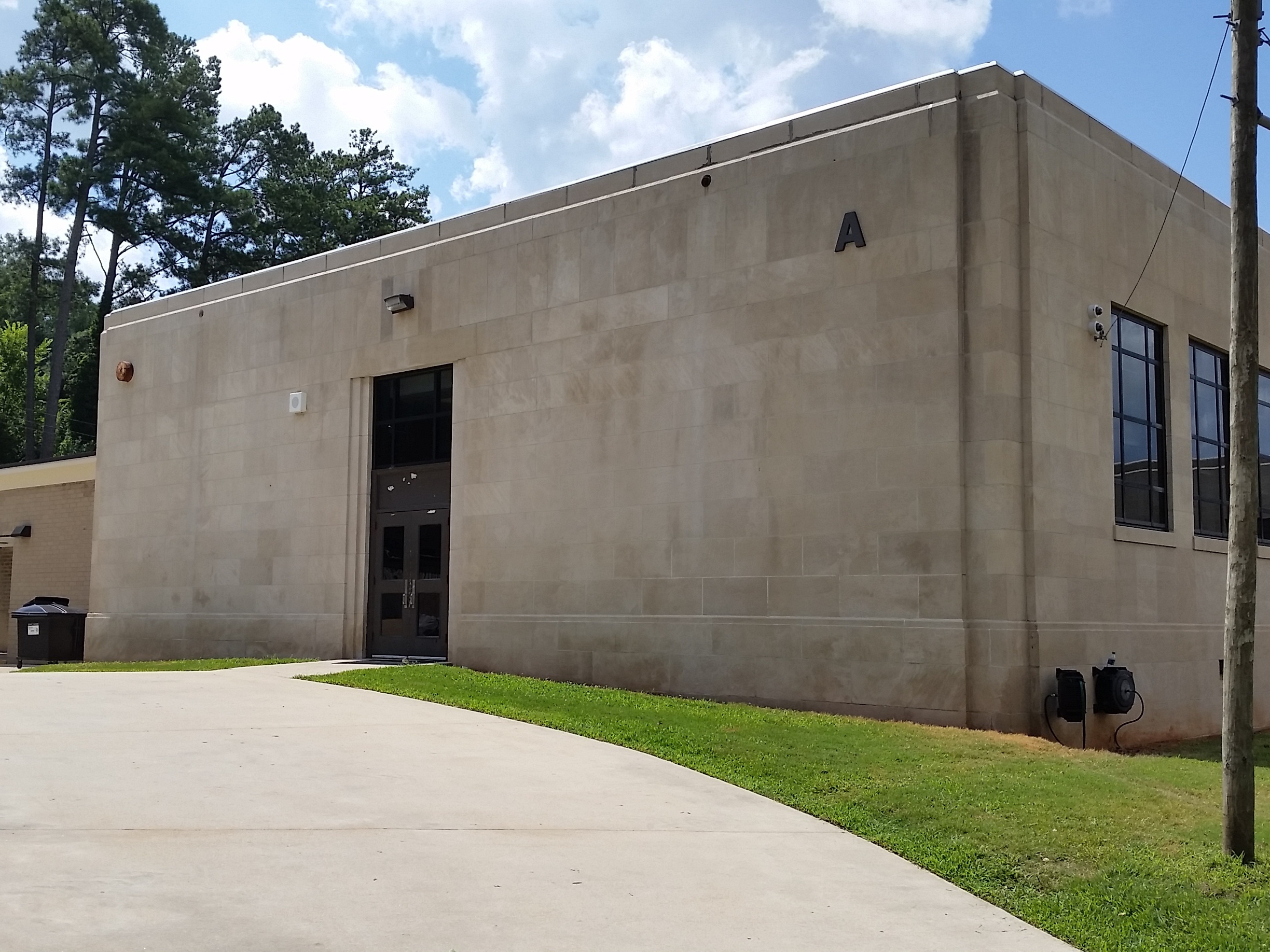
Working in a Confined Space is High-Risk Work
OSHA defines a confined space as any space that:
- Is large enough that an employee can enter and perform work
- Has limited or restricted means for entry or exit
- Is not designed for continuous employee occupancy
OSHA Permit-required Confined Space:
- Contains or may contain a hazardous atmosphere
- Contains a material that has the potential for engulfing an entrant
- Is shaped such that an entrant could be trapped or asphyxiated
- Contains any other serious safety or health hazards
When we send one of our Blackwell’s associates into a confined space, we monitor the air continuously, and we send someone that's OSHA trained to work in tight, dangerous places.
Not only is the associate trained and equipped with all the equipment he needs to keep him safe, but he has an OSHA trained support crew topside to get him out safely if an accident happens.
Confined Spaces include tanks, storage bins, pits, silos, ovens, and ductwork
25% of confined spaces have hazardous air. 50% of deaths in confined spaces result from oxygen deficiency (or limited air supply) and no air monitoring.
Blackwell’s, Inc. Protocol for Safety in Confined Spaces:
- Complete Confined Space Permit
- Control the Access Zone (barricades/fall protection)
- Monitor the air quality with Multi Gas Detector (O2, H2S, CO, LEL)
- Provide natural or mechanical ventilation as needed
- PPE required: Tyvek suit, gloves, eye and ear protection, dust mask (or APR/SAR if needed)
- Vertical work: tripod, winches, safety harness
- Horizontal work: anklets attached to safety retrieval line
- Attendant: continuously observes and communicates with entrant
4 Basic Steps We Take to Protect Our Associates
- Identify any confined spaces in the workplace
- Risk assessment of all hazards in those confined spaces
- Take all necessary steps to mitigate the identified hazards
- Put in to place an established rescue plan for emergencies
Completing the Confined Space Permit prior to entry (notice the yellow Multi Gas Detector).
Entering the confined space of a silo. Take note of the tripod, safety harness, two winches and two cables, PPE, ventilation for the entrant, and the harnessed safety attendant. (After)
Inside the confined space of a 110 ft. silo. Two cables, connected to separate winches, are used in silo work. One cable supports the bosuns chair with the entrant seated. The second cable is connected to the safety harnessed entrant.
Cooling towers are specialized heat exchanging devices to cool water and dissipate heat to the atmosphere.
For plants in continuous production, these systems require preventive maintenance.
Problems associated with cooling water systems:
- Corrosion from oxidation of the metal components of system
- Scale buildup from precipitation of minerals in water
- Fouling from dust and corrosion by-products
- Microbial contamination (bacteria, yeasts, fungi, algae) creating waste deposits (microbial slime) and potential contagions (e.g. Legionella)
- Animal excrement buildup (e.g. pigeons) and disease associated with atomization and respiration of contaminated water
These problems affect the system by:
- Increasing maintenance costs
- Increasing the frequency of shutdowns for repair and/or replacement of components
- Decreasing the cooling efficiency and increasing energy consumption
- Posing a potential liability associated with illness due to lack of cleaning or maintenance of the cooling tower